FEATURED MANUFACTURING SERVICES
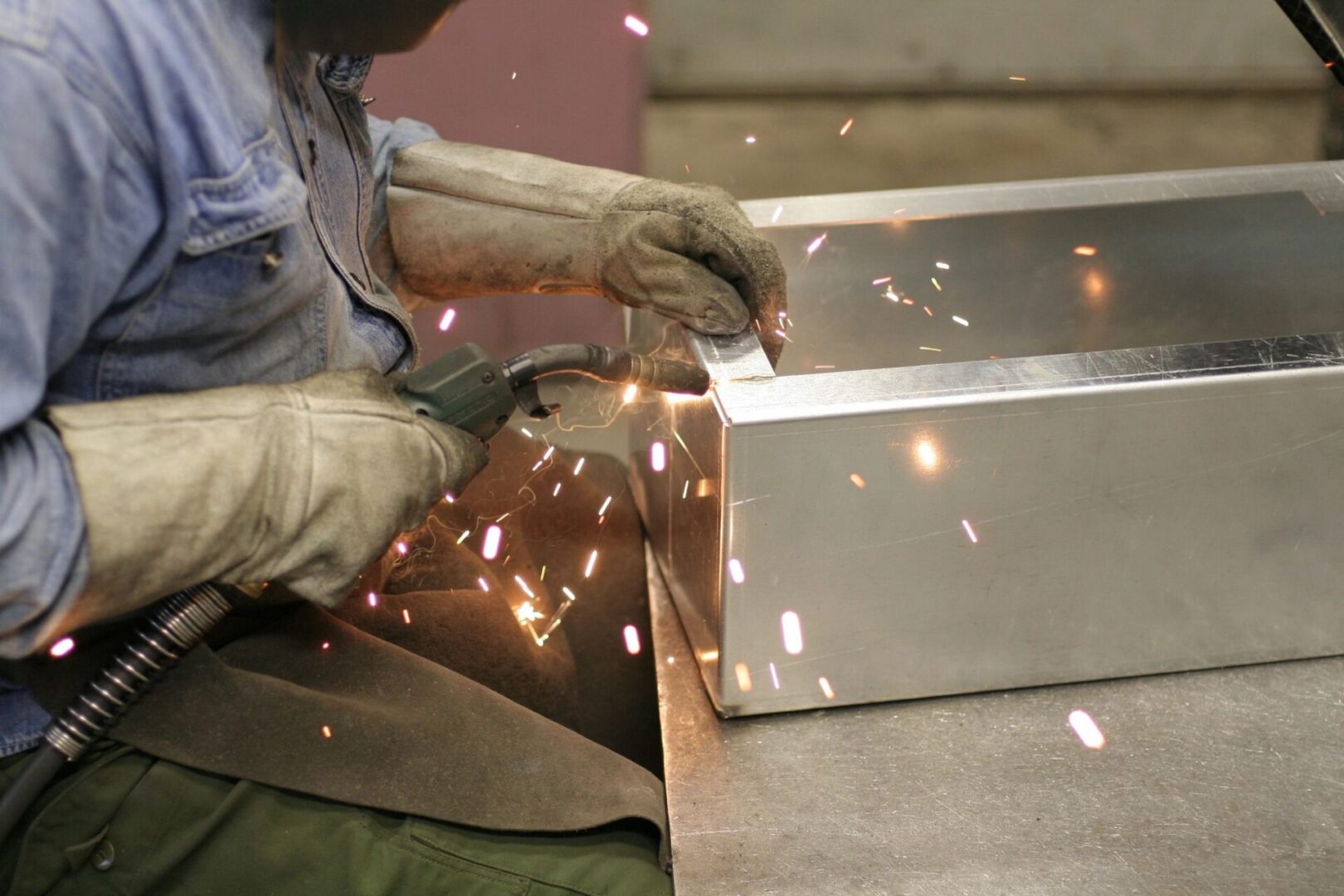
Identify appropriate processes and supply chains to build prototypes in order to identify potential issues, and optimize performance before full-scale production.
Assess the technical, economic, and logistical feasibility of manufacturing proposed engineering projects.
Communicate and report on manufacturing intents, requirements, and guidelines effectively to stakeholders, manufacturing teams, and other collaborators.
Process Optimization
Develop, improve, and optimize manufacturing processes to enhance efficiency, productivity, and quality by identifying bottlenecks, inefficiencies, and areas for improvement through data analysis and process monitoring.
Analyze production capacity and demand forecasts to plan for future growth and expansion. Assess the need for additional resources, facilities, processes or equipment to support increased production volumes or new product introductions and iterations.
Develop production plans and schedules based on demand forecasts, inventory levels, and production capacity. Coordinate with manufacturing teams to ensure efficient use of resources and timely production execution.
Research and identify suitable manufacturers, suppliers, and subcontractors capable of meeting client requirements.
Collaborate with suppliers to ensure timely delivery of materials, components, and finished products by monitoring inventory levels, tracking shipments, and addressing any logistics or transportation issues that may arise. Evaluate supplier performance, negotiate contracts, and resolve quality or delivery issues to maintain a reliable supply chain.
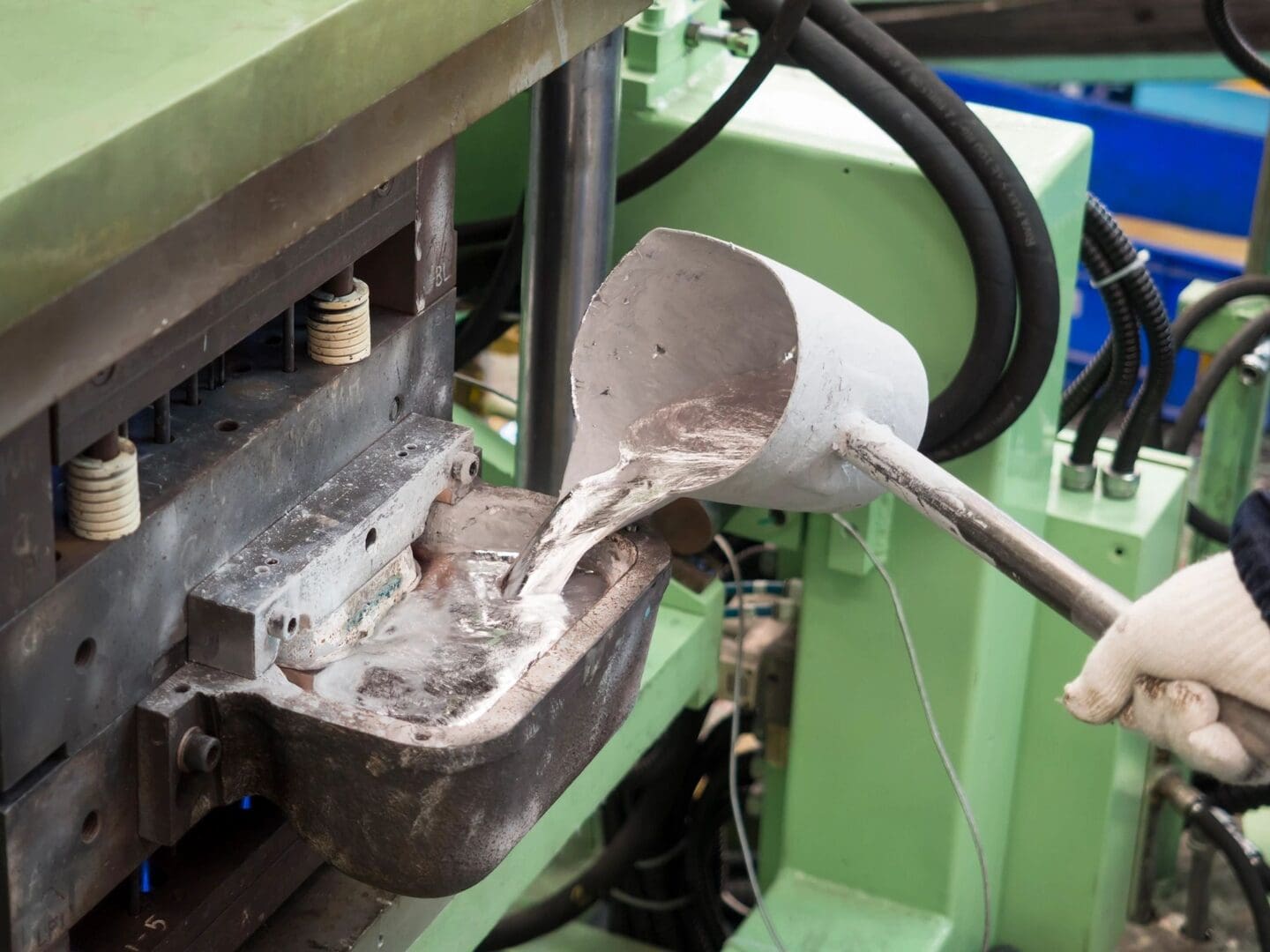
Cost Estimation and Budget Management
Estimate manufacturing costs and provide cost projections, manage project budgets, track expenses, and identify opportunities for cost savings through negotiation and process optimization.
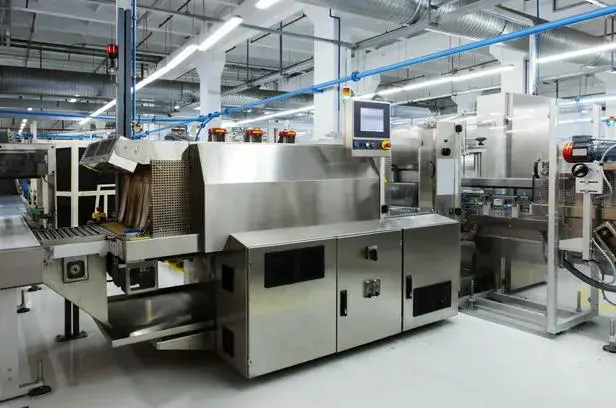
Develop and implement quality assurance processes and controls to maintain product quality and reliability. Conduct inspections, audits, and testing to ensure compliance with quality standards and regulatory requirements.
Identify potential risks and vulnerabilities in the supply chain, develop strategies to mitigate them, and anticipate and plan for disruptions.
Develop sourcing strategies to optimize costs, minimize risks, and ensure continuity of supply of raw materials, components, and parts.